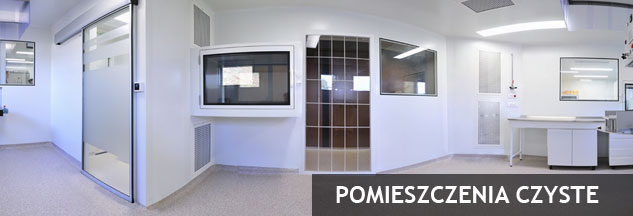
Pomieszczenie czyste (cleanroom) to obszar o ustalonym sposobie kontroli zanieczyszczeń cząstkami i drobnoustrojami w środowisku, zbudowany i użytkowany w sposób ograniczający wprowadzanie, powstawanie i gromadzenie się zanieczyszczeń.
Pomieszczenia czyste praktycznie zawsze składa się z dwóch podstawowych i nieodłącznych części:
• przestrzeni oddzielonej przy pomocy elementów budowlanych tak, że jest odizolowana od zewnętrznego środowiska
• jednostki klimatyzacyjnej, wyposażonej w skuteczną filtrację powietrza. Jednostka klimatyzacyjna jest zwykle wyposażona w urządzenie ogrzewające, urządzenie chłodzące i parowy nawilżacz oraz kilkustopniową filtrację powietrza. Kluczową częścią systemu filtracji są filtry HEPA.
Powietrze jest tłoczone do wnętrza pomieszczeń czystych poprzez specjalny układ filtrów, eliminujących kolejne frakcje zanieczyszczeń. Całe powietrze wewnątrz pomieszczenia jest ciągle filtrowane przez zestaw filtrów HEPA w celu usuwania zanieczyszczeń powstałych wewnątrz. Urządzenia wewnątrz pomieszczeń czystych muszą być specjalnie zaprojektowane tak, aby nie generowały dodatkowych zanieczyszczeń. Pomieszczenia czyste wykonane są z materiałów zapewniających gładkich i łatwozmywalnych, odpornych na substancje używane w procesie produkcji i na środki czyszczące.
Cząstki w powietrzu
Ilość cząstek/m3 w zewnętrznym powietrzu | |||
Wymiar | Brudne | Normalne | Czyste |
>0.1µm | 10 000 000 000 | 3 000 000 000 | 500 000 000 |
>0.3µm | 300 000 000 | 90 000 000 | 20 000 000 |
>0.5µm | 30 000 000 | 7 000 000 | 1 000 000 |
Pomieszczenia czyste, w których wytwarzane są produkty sterylne, są klasyfikowane w zależności od wymaganej charakterystyki środowiska. Dla każdej operacji wytwórczej wymagany jest odpowiedni poziom czystości środowiska, co ma na celu zminimalizowanie ryzyka zanieczyszczenia produktu lub stosowanych materiałów.
W celu spełnienia w tych pomieszczeniach wymagań dotyczących czystości powietrza, należy je określić "w działaniu" i "w spoczynku".
Jako stan "w spoczynku" rozumiana jest sytuacja, gdy zainstalowane są wszystkie urządzenia produkcyjne i znajdują się one w stanie gotowości do podjęcia produkcji, ale obsługa nie jest obecna w pomieszczeniach.
Stan "w działaniu" to sytuacja, gdy wszystkie urządzenia funkcjonują w odpowiedni sposób
i są obsługiwane przez przewidzianą liczbę pracowników.
Przy wytwarzaniu sterylnych produktów farmaceutycznych wyróżnia się cztery klasy czystości powietrza:
Klasa A | wydzielona strefa, w której wykonywane są czynności największego ryzyka, np. napełnianie, zamykanie korkami, wykonywanie aseptycznych połączeń, oraz miejsce, gdzie znajdują się otwarte ampułki i fiolki. Zwykle odpowiednie warunki pracy zapewnia laminarny przepływ powietrza. Systemy laminarnego przepływu powietrza powinny zapewnić jednorodną szybkość przepływu powietrza w miejscu |
Klasa B | przy produkcji aseptycznej i napełnianiu strefa ta stanowi środowisko otaczające dla klasy A; |
Klasy C i D | pomieszczenia czyste, w których przeprowadza się mniej krytyczne etapy wytwarzania |
Przykładowe czynności, które mogą być wykonywane w pomieszczeniach określonej klasy, podano w tabeli:
Klasa | Przykładowe czynności wykonywane dla produktów z końcową sterylizacją |
Klasa A | Napełnianie opakowańproduktami, kiedy występuje wyjątkowe ryzyko, naważanie produktów |
Klasa C | Przygotowanie roztworów, kiedy występuje wyjątkowe ryzyko. Napełnianie produktami. |
Klasy D | Przygotowanie roztworów i składników do późniejszego napełniania |
Klasa | Przykładowe czynności wykonywane przy produkcji aseptycznej |
Klasa A | Przygotowanie i napełnianie aseptyczne |
Klasa C | Przygotowanie roztworów, które będą filtrowane |
Klasy D | Postępowanie z komponentami po myciu |
Klasyfikacja pomieszczeń czystych według norm, ma na celu określenie ilości cząstek znajdujących się w powietrzu, a następnie sklasyfikowanie powietrza zgodnie z klasami czystości ISO lub wymaganiami polskimi (tabela).
Klasyfikacja pomieszczeń czystych może odbywać się w trzech stanach: po wybudowaniu, w stanie spoczynku, w stanie pracy.
Podział na 9 zdefiniowanych klas ISO odpowiada (w stanie spoczynku) następującym klasom zgodnie z GMP/PIC-Guide:
klasa „A” i „B” – ISO-Class 5;
klasa „C” – ISO-Class 7;
klasa „D” – ISO-Class 8;
W Polsce obowiązują klasy czystości z Rozporządzenia Ministra Zdrowia z dnia 2 października 2006 r. w sprawie wymagań Dobrej Praktyki Wytwarzania (Dz.U.06.194.1436), oparte o wytyczne GMP/PIC-Guide. Rozporządzenie to przewiduje również pomiary ilości cząstek w stanie pracy. Maksymalne dopuszczalne ilości cząstek w zależności od klasy czystości badanego powietrza przedstawia tabela
Maksymalna dopuszczalna liczba cząstek w 1m3 powietrza | ||||
Klasa czystości | w stanie spoczynku | w stanie pracy | ||
≥0.5µm | ≥5.0µm | ≥0.5µm | ≥0.5µm | |
A | 3 500 | 1 | 3 500 | 1 |
B | 3 500 | 1 | 350 000 | 2 000 |
C | 350 000 | 2 000 | 3 500 000 | 20 000 |
D | 3 500 000 | 20 000 | nie określona | nie określona |
Liczba cząstek podana w tabeli dla stanu "w spoczynku" powinna być uzyskana po krótkim czasie oczyszczania powietrza (15-20 min., wartość zalecana) po zakończeniu operacji, gdy w pomieszczeniu nie ma już ludzi. Liczba cząstek dla klasy A przedstawiona w tabeli dla stanu "w działaniu" powinna być zachowywana w strefie bezpośrednio otaczającej produkt zawsze wtedy, gdy produkt lub otwarte opakowanie jest narażone na kontakt ze środowiskiem zewnętrznym. Dopuszczalny jest fakt, że nie zawsze jest możliwe wykazanie zgodności z obowiązującymi standardami dotyczącymi liczby cząstek w miejscu napełniania, z powodu tworzenia cząstek lub kropel z samego produktu.
Pomiar ilości cząstek wykonuje przy użyciu miernika cząstek, ilość punktów pomiarowych wyznacza pierwiastek z powierzchni pomieszczenia. Wyniki uzyskane podczas pomiaru stanowią podstawę do dokonania niezbędnych obliczeń statystycznych. Warunkiem spełnienia klasy czystości w danym pomieszczeniu jest uzyskanie następujących wyników pomiarów:
• Stężenia cząstek w punktach pomiarowych są niższe od limitu stężenia dla danej klasy pomieszczenia
• Górna granica poziomu ufności średniej (UCL 95%) jest niższa od limitu stężenia dla danej klasy pomieszczenia
Klasyfikacja ilości cząstek wg. obowiązujących standardów:
Rozp. MZ/ cGMP |
SI Fed.Std. 209e |
Ang. Fed.Std. 209d |
PN-EN ISO 14644-1:2005 |
Maksymalna dopuszczalna liczba ziaren/m3 równych lub większych niż podana wielość |
|||||
0,1µm | 0,2µm | 0,3µm | 0,5µm | 1,0µm | 5,0µm | ||||
ISO Class1 | 10 | 2 | - | - | - | - | |||
ISO Class2 | 100 | 24 | 10 | 4 | - | - | |||
M1 | 350 | 75,5 | 30,9 | 10 | - | ||||
ISO Class3 | 1000 | 237 | 102 | 35 | 8 | - | |||
M 1,5 | | | 1240 | 265 | 106 | 35.3 | ||||
M2 | 3.500 | 757 | 308 | 100 | - | ||||
ISO Class4 | 10.000 | 2.370 | 1.020 | 352 | 83 | - | |||
M 2,5 | 10 | 12.400 | 2.650 | 1.060 | 353 | - | |||
M3 | 35.000 | 7.570 | 3.090 | 1.000 | - | ||||
A / B | 3.500 | 1 | |||||||
ISO Class5 | 100.000 | 23.700 | 10.200 | 3.520 | 832 | 29 | |||
M 3,5 | 100 | 26.500 | 10.600 | 3.530 | - | ||||
M4 | 75.700 | 30.900 | 10.000 | - | |||||
ISO Class6 | 1.000.000 | 237.000 | 102.000 | 35.200 | 8.320 | 293 | |||
M 4,5 | 1000 | 35.300 | 247 | ||||||
M5 | 100.000 | 618 | |||||||
C | 350.00.0 | 2.000 | |||||||
ISO Class7 | 352.000 | 83.200 | 2.930 | ||||||
M 5,5 | 10.000 | 353.000 | 1 | 2.470 | |||||
M6 | 1.000.000 | 6.180 | |||||||
D | 3.500.000 | 20.000 | |||||||
ISO Class8 | 3.520.000 | 832.000 | 29.300 | ||||||
M 6,5 | 100.000 | 3.530.000 | 24.700 | ||||||
M7 | 10.000.000 | 61.800 | |||||||
ISO Class9 | 35.200.000 | 8.320.000 | 293.000 |